Imagine a site with multiple fuel tanks and dispensing stations. Imagine the logistics of daily stick and totalizer readings and the readings required when fuel is delivered from the supplier.
A bummer, to be sure, especially if it's the way you are currently set up.
Now imagine the tanks are monitored with electronic-level probes. Combine this with the convenience of the pump dispenser totalizers automatically recorded along with recordings of the fuel dispensed at each pump. What would life be like when all of these measurements are sent to a platform in the cloud, and your inventory reconciliation is automatically calculated? Imagine pouring a cup of coffee and printing out your inventory reconciliation report as you relax and enjoy your morning cup of java.
Welcome to the world of SM2's automated fuel inventory management.FUEL INVENTORY RECONCILIATION—AUTOMATING THE PROCESS
In the first of this 3-part blog series, we went over the fundamentals of fuel inventory management, while part 2 was all about tracking off-site storage tanks. Now, we're going to tie it all together.
Get your fuel inventory management reports with a single click, whether you have USTs or ASTs—underground and aboveground storage tanks, respectively. Never run out of fuel again, and catch leaks or other discrepancies immediately, so the process of identifying the problem is much easier. Always be on top of your fuel inventory reconciliation regardless of staff schedules, holidays or absent personnel.
With an automated system, you can balance your inventories daily instead of weekly or monthly. This will allow you to catch discrepancies quickly. These discrepancies are more easily resolved if identified the next day instead of the following week or at the end of the month.
If your supplier is delivering fuel while pumps are dispensing fuel to fleet vehicles, the automated fuel management system keeps calculations precise and accurate. No more second-guessing your manual calculations.
Monitoring of your fuel inventories for all your sites can be controlled and displayed from a central, dynamic dashboard that is customizable to how you operate. Aggregate and filter information from different sources into ad hoc views, which you can define and save for frequent use.
You can automate your reports and send them directly to the team members needing them. Get notified when inventories run low or, better yet, have automated notifications sent directly to your supplier.
Without a doubt, SM2's automated fuel inventory management makes your fleet life easier, whether you have above-ground or underground storage tanks.
Fuel Reconciliation—Underground Storage Tanks
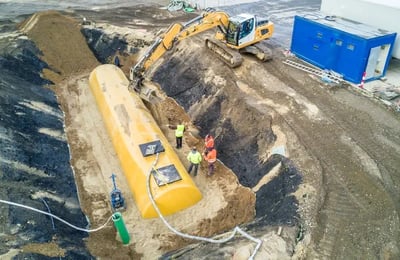
Let's take a closer look at the types of reports available. First, we'll
address the elephant in the room: the daily reports required by the local authorities for USTs. This particular report has been customized to suit the requirements of a specific local authority. Your local authorities may require a slightly different variation on how the information must be reported, but fear not: the report can be customized based on your government's requirements.
Let's investigate the report in more detail.
This is a typical report for a one-month period. The image displays the records for the first two weeks. Columns A & B automatically record the pump totalizers, with column C calculating the dispensed quantity. Column D shows the automatic tank probe readings, and Column E shows the fuel delivered by the supplier. The estimated inventory in column G is compared to the measured inventory levels in column F. The deviation is calculated in column H.
The above image is the bottom half of the monthly report with the total dispensed quantity, the total delivered quantity for that month, calculated deviation, the number of days where losses occurred, the percentage deviation, and other information required by the local authorities. This report is customized to the requirements of local authorities and can be printed or emailed electronically at the required reporting intervals.
This solution is accurate regardless of what is happening in terms of fuel deliveries and fuel dispensed to your fleet assets during those deliveries. Daily measurements and readings are taken at the same time each day, and that schedule is unaffected by weekends and vacation periods. Leaks from storage tanks or associated piping will be quickly identified. This can minimize what could be a massive environmental disaster and keep the contaminated plume to a minimum. This is all in addition to eliminating the time you'd otherwise waste collecting tank levels using dipsticks and going through the arduous process of manual fuel inventory reconciliation.
Managing Your Fuel Reconciliation Data Reports - Aboveground Storage Tanks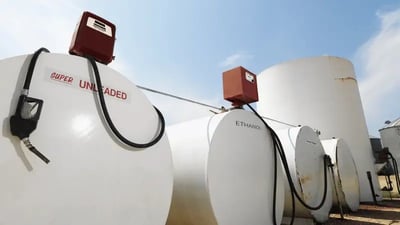
An automated fuel reconciliation solution can also benefit the fleet manager with above-ground storage tanks. Above-ground storage tanks may be subject to U.S. EPA’s Spill Prevention, Control, and Countermeasure (SPCC) regulation (40 CFR Part 112). So, while the environmental regulations for ASTs differ from USTs, you still need to:
- Maintain accurate records of your daily levels in each storage tank
- Accurately record the additional fuel added from your supplier
- Track what amount is dispensed to which vehicle/asset—when and by whom
As a fleet manager, whether you manage below or above-ground tanks, leaks are the main risk you must be concerned with. Water and soil contamination from a leaking tank is detrimental to the environment and devastating to your organization’s bottom line and corporate reputation. The cleanup costs can be astronomical if the leak goes undetected for a long time. Such a leak could force the evacuation of nearby buildings and neighborhoods. Beyond these already massive damages, property values decrease because of the event. And last but certainly not least, you will see a sizeable increase in your insurance premiums.
Accurate daily measurements are essential in quickly identifying a potential leak. An automated fuel inventory system virtually eliminates the man-hours involved in collecting data from separate tanks at several sites with multiple fuel types. Any discrepancy identified that day is much easier to investigate and resolve than identifying a potential issue a week or two later—or even worse, at the end of the month.
An ideal daily fuel tank monitoring report provides measurement levels and can report the recorded levels and reading for any given period—a specified day, week, month, or year. The report is dedicated to a single site and a single product. That means if you have one site with three diesel storage tanks and one unleaded fuel tank, the system should produce two reports for that specific site for that day, one for diesel and the second for unleaded. In a multi-site operation, you'd get reports on one site and one product at a time.
Let’s look at an example report and review what information it provides and what we can do with this information.
The Inventory Reconciliation period is stated in the top right corner. Again, this can be daily, weekly, monthly, yearly, or any predefined period of time. This report is for one site (Site: S007 - NTC) and one product which, in this case, is diesel. There are two diesel fuel storage tanks: # 01 and 02.
The report contains readings from three separate sources:
- Consumption Calculated Using Inventory Variations: Tank level readings are recorded for the beginning and end of the reporting period. Additionally, all deliveries to each tank are listed so consumption can be calculated by the system. This consumption is used as the reference amount 281,913.80 (Liters).
- Consumption Calculated Using Fueling Transactions: Each pump dispensing the same product (diesel) is totalized for the period. At the site in this example, there are two diesel pumps. These volumes can be captured automatically with your fuel management system and/or manually. We have a reported total of 279,536.70 (Liters), which is a -0.8% deviation from the consumption calculated using the tank gauging system. So, which calculated volume is correct? Let's have a look at the third calculation.
- Consumption Calculated Using Pump Totalizer Readings: The third section of the report provides dispenser pump totalizer readings for both pumps at the site. We notice that the total consumption for the period is 279,548.10 (Liters), which is a -0.8% deviation from the reference amount, i.e. what was calculated using inventory variations in the first section above.
You can quickly see that the issue may be with the gauging system or the distribution piping to the pumps since the totals from the fueling transactions and the totalizers match up. Could it be a leak in the tank or the pipes? Could the fuel drops have been miscalculated? Are the level probes out of calibration or, in the case of manual stick readings, is there an issue with that process?
A sound fuel management system solution provider should also have a fully trained and qualified support staff that is a phone call away to help assist you with potential issues and how to verify the exact problem.
Fuel Tank Inventory Reconciliation— Conclusion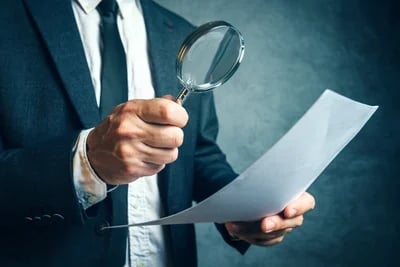
Regardless of whether you have above-ground or underground tanks, capturing level and totalizer readings should be done daily to identify leaks quickly and rectify the issue promptly before it becomes a significant problem. If this process is performed manually, consistent and accurate readings and calculations become a significant challenge due to human error and negligence. Manual methods also increase costs as they require additional administrative labor to carry out.
When the fuel inventory reconciliation process is fully automated, reports can be generated daily with a single click—and sometimes even less than that!
Over a cup of coffee, you can review reports and identify any discrepancies. If a deviation in total consumption exists, the data is right there to help point you in the right direction. If there is doubt, a good system provider will have trained and qualified support to help you identify where the issue lies and what to do to correct the situation quickly.
Final Fleeting Thought
Fuel can account for 30% to 60% of your operational budget. Since the price of fuel is out of your control, the only way of ensuring efficient use of this resource is thorough, end-to-end monitoring.
For over 30 years, Coencorp has been providing fuel inventory management solutions to a wide variety of industries, from the transit and public works departments to mining and construction. SM2-FUEL is the result of decades of evolution and development based on real-world installs and feedback.
Looking to get a handle on your fleet fuel consumption and make your fuel inventory management more accurate and efficient? Check out the fuel inventory management product page or give us a call at 1-866-263-6267. We will work with you to ensure you can account for every drop of fuel spent.