Fuel is the blood coursing through the veins of industrial fleets. It's what puts the "moving" in your moving assets. As a fleet manager, fuel is a major area of focus of yours and an omnipresent preoccupation. The often unpredictable rise in fuel costs further complicates your already difficult job.
Nonetheless, comprehensive control over your fuel inventory and consumption is essential to ensure profits and avoid losses, and as you know, that's no simple task. There’s just so much to consider: Where’s your fuel going? How much fuel is being purchased? Does it match what was delivered to your storage tanks? Is there shrinkage in your storage tanks and fleet distribution, and what’s the cause?
Suppose regulatory authorities or chief executives requested your fuel reconciliation reports. How confident are you in your capacity to quickly provide daily, weekly, monthly, and annual numbers with the certainty that the information is correct? These questions can be as daunting as they are essential.
Manual Fuel Reconciliation—Too Much Room for Error
Traditional fuel inventory management methods involve manual tank dips, manual tank level gauging, and manual record keeping. This is outdated, time-consuming, and prone to error. Many fleet managers go through a long, tedious process of manually milling over spreadsheets and scrutinizing and scrubbing errors from manually entered data to get the detailed information they need; this is not anyone's cup of tea, not to mention a drain on your valuable time—and for what outcome? We're unsure if any fleet manager relying on these manual processes can ever be fully secure in their data sets.
Maybe that’s what’s brought you here today.
Ultimately, fuel accounts for a significant portion of a fleet’s operating budget, and one of the main objectives of fuel management is controlling costs. To that end, there's no way around the need for accurate fuel inventory reconciliation. True, you can't control fluctuating fuel prices, but you can mitigate fuel costs by precisely monitoring where and how much of it is being used.
In this instalment of Fleeting Thoughts (the first of a 3-part series), we discuss the problems inherent to manual fuel reconciliation and the production of related reports. If you’ve been pondering the efficiency of your fuel inventory management, read on to learn why you should leave those outdated and painful manual processes behind.
The Process of Fuel Inventory Reconciliation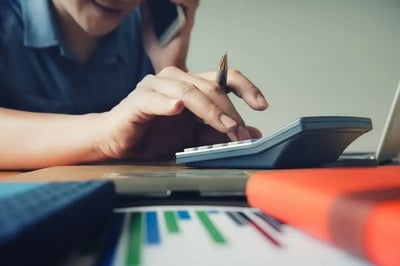
Fuel inventory reconciliation is time-consuming and surprisingly difficult to get right. Manually keeping accurate records of fuel inventory, fuel drops, and fuel dispensed is challenging and rife with opportunities for errors and discrepancies. The problem compounds when multiple fuel storage/dispensing systems need to be tracked; it further complexifies in proportion to fleet size, number of vehicles and of vehicle classes, and whether other asset types draw on fuel reserves.
To get a feel of the challenge, it helps to start by reviewing the core idea and the data elements involved. At its heart, fuel inventory reconciliation is simplicity itself; in any given time period, we should confirm that:
Fuel bought - Ending inventory = Fuel consumed
Of course, that only holds if your storage tank is empty at the outset. Refining to account for this still yields a simple formula:
Starting inventory + Fuel bought - Ending inventory = Fuel consumed
Now your fuel yard may house several storage tanks, say, T1, T2, and T3:
Fuel consumed = Starting inventory(T1) + Starting inventory(T2) + Starting inventory(T3) + Fuel bought -Ending inventory(T1) - Ending inventory(T2) - Ending inventory(T3)
Your organization might have several fueling sites, say, S1, S2, S3, and S4, each ordering fuel deliveries according to their needs:
Fuel consumed =
Starting inventory(S1T1) + Starting inventory(S1T2) + Starting inventory(S1T3)
+ Starting inventory(S2T1) + Starting inventory(S2T2) + Starting inventory(S2T3)
+ Starting inventory(S3T1) + Starting inventory(S3T2) + Starting inventory(S3T3)
+ Starting inventory(S4T1) + Starting inventory(S4T2) + Starting inventory(S4T3)
+ Fuel bought(S1) + Fuel bought(S2) + Fuel bought(S3) + Fuel bought(S4)
- Ending inventory(S1T1) - Ending inventory(S1T2) - Ending inventory(S1T3)
- Ending inventory(S2T1) - Ending inventory(S2T2) - Ending inventory(S2T3)
- Ending inventory(S3T1) - Ending inventory(S3T2) - Ending inventory(S3T3)
- Ending inventory(S4T1) - Ending inventory(S4T2) - Ending inventory(S4T3)
As you can see, things start to get a bit hairy.
Furthermore, the above number-crunching only yields your fleet's fuel consumption according to inventory variations, and that’s just half the story. You still need to compare this figure to your fleet's fuel consumption according to fueling transactions, that is, the volume of product distributed during the same period to various equipment tallied from each dispenser across all fueling yards in your operations.
Hand-collecting all this data daily, demands a level of dedication and resources that few organizations are able or willing to commit. And many fleet managers will have to deal with additional headaches, such as:
- EPA accountability requirements for Underground Storage Tank (USTs) reconciliation
- Fuel distribution tracking of mobile fuel trucks (or bowsers)
- Transfer tanks (A.K.A. saddle tanks or slip tanks)
- Jerrycans and small gas-powered tools such as lawnmowers, chainsaws, etc.
Let’s dive into the core issue of reconciling primary storage tanks (we’ll review the key challenges of tracking fuel further down the operations chain in part 2 of this mini-series).
Challenges with inventory reconciliation in primary fuel storage tanks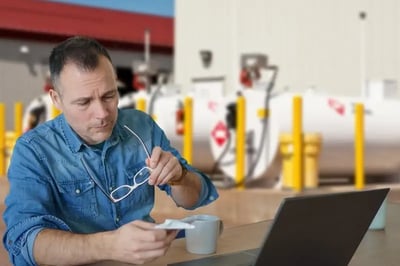
Fleet fuel is stored in two principal ways: above and underground storage tanks. Regardless of storage mode, maintaining adequate fuel levels is paramount for operations and production. Dealing with fuel inventories requires strict discipline and precision, and fleet managers face several significant challenges. When multiple tanks come into play, the logistics of proper record-keeping become even more difficult:
- What happens if the daily recording routine is missed?
- How do you keep tabs on fuel deliveries from suppliers?
- How do you satisfy environmental reporting requirements?
These are but a few of the questions you face as a fleet manager. Let's look at some of the specifics.
- Getting snapshot readings is necessary yet difficult in dynamic fleet environments. As previously stated, proper fuel inventory reconciliation requires that tank level variations match totalizer readouts of associated dispensers. Therefore, you must simultaneously record the dispensers' totalizers and the tank level measurements. The longer the time elapsed between these two readings (say, tank levels are measured in the morning and dispenser totalizers in the afternoon) the more likely discrepancies will be introduced due to product being dispensed during that time gap.
- Manual record-keeping is laborious and time-consuming. Then you need to record the measurement values. This takes some time. So does keying the information into a spreadsheet and reviewing the data for errors. The person in charge of this is also responsible for other aspects of your operations, and their time is valuable. Situations will arise when other matters take precedence over the tedious task of daily fuel reconciliation reports, compromising the accuracy of your fuel reconciliation.
- Consistent record-keeping is key—the more days you miss, the harder it becomes to figure out where disparities are coming from. You must strive to ensure that fuel tank levels and dispenser totalizers are recorded daily; it's hard enough to find out what went wrong yesterday, never mind a month ago. Scheduling conflicts, sick leave, vacation, or simply being too busy that day: there are many reasons why daily readings are missed. And typically, backup personnel tend to be less diligent about it when they're needed. What if storage tanks aren't dipped over the weekend? Come Monday morning; your operation could be running on fumes.
- The logistics get exponentially complicated the larger the scale of your operation. Maintaining and reconciling fuel records becomes significantly more difficult when various tanks and fuel dispensers are located in separate yard areas—and maybe multiple locations. Aggregating, cleansing, and consolidating data from fuel yards dispersed throughout the city, state, or country, all while activities are in progress, is easier said than done.
- Even trusted fuel suppliers must be verified. “Trust but verify," as the saying goes. Generally, fuel suppliers are reliable and trustworthy. But mistakes happen, instruments become defective, and receipts get misplaced: how can you be sure that your supplier delivered the exact amount of fuel on the invoice? It's only possible if you keep precise inventory records. If your management team asks, can you prove you’re keeping deliveries in check?
- Regulatory agency reporting is a constant and nagging preoccupation. Depending on the jurisdiction, local and regional government authorities may require regular monthly or annual reports. Your management will also want regular updates on fuel consumption. Each report is unique in how the information is formatted and delivered, and preparing them is stressful, even more so if any information is missing or not readily available.
- Undetected leaks in USTs can be devastating financially, environmentally, and reputationally.
While above-ground storage tanks (ASTs) take up some yard space and, if we're honest, are a bit of an eyesore, they have the advantage of containment bases and walls, confining eventual leaks to a finite area and protecting the area. Plus, leaks are just easier to see with ASTs. Underground Storage Tanks (USTs), however, are more serious business.
According to the EPA, over half a million USTs containing petroleum or other chemicals exist in the United States alone. Thousands of these tank systems and associated piping are currently leaking, making them an environmental and safety risk. It’s why federal, state/provincial, and municipal authorities have daily fuel UST reconciliation regulations to identify leaks and mitigate ecological damage quickly.
What happens if an underground tank leak goes undetected for several days (think long weekend)? It may be too late to mitigate the damage. Severe consequences loom for the environment, public health, property values, and fleet operations if leaks aren’t caught in time. They can contaminate groundwater supplying drinking wells and cause a buildup of vapors in underground structures. A tank leak can shut down your site, result in cleanup costs running in the hundreds of thousands, and, if the contamination plume reaches the water table, it may require years of groundwater remediation—a significant financial burden and loss of reputation.
Clearly, disparities between UST "stick inventory" and "book inventory" need to be tracked and scrutinized daily, and these data must be preserved for at least a year. Doing this adequately represents significant time and financial commitments. There isn't much room for error.
Final Fleeting Thoughts
From fuel tanks to fleets, there’s a lot for any fleet manager to deal with when it comes to fuel. In this instalment of a 3-part series, we reviewed the work involved and how it escalates with multiple tanks and sites, EPA requirements, and mobile assets. Done manually, fuel reconciliation and data reporting are time-consuming and prone to error, with many fleet assets commonly being neglected. Yet, to identify where fuel efficiency can be improved and savings increased, you must track every asset diligently and consistently.
An automated fuel reconciliation system can help you get a handle on where your fuel is going, quickly detect leaks, and make reporting effortless. It enables you to pinpoint where you will get the best ROI in fuel-saving measures—things like fuel efficiency technology, driver behavior training, and scheduled asset maintenance. Most importantly, you’ll never have to worry about having adequate fuel reserves to run your operations.
Bottom line: to avoid losses and possible environmental damage and maximize profits, you need to account for every drop of fuel spent. There’s no better way to do that than with an automatic fuel management system like Coencorp’s SM2 Fleet Management System.
Check out part 2 of our 3-part series on fuel inventory management: tracking off-site fleet fueling