In the mining industry, fuel consumption is high volumes, high stakes, and most definitely not a game.
Mining companies need to continuously reinvent themselves and look to improve their operating efficiencies in the area of fuel consumption to stay profitable. There are many options available for mine operators to implement to improve fuel efficiencies and reduce overall fuel consumption. The challenge is to accurately track and monitor the fuel used at the overall mining site and reconcile fuel consumption by an asset. You can’t manage what you can’t measure.
A robust, integrated automatic fuel management system can accurately track fuel consumption by asset so continuous improvement projects can be evaluated effectively. Coencorp’s SM2-FUEL management solution offers the capability to track fuel deliveries and consumption by asset in a challenging mining environment.
Fuel Challenges Of Mining Fleet Management
Haul Trucks
As mines age, operations face the reality of mining low-grade ores. For opencast mining companies, near-surface ores are becoming depleted, forcing deeper digging, which in turn increases the ore hauling distance. Larger haul trucks are being deployed to transport more tons of ore per trip; however, they add to the fuel consumption—especially as the equipment travels at higher grades. Some large haul truck manufacturers estimate the fuel consumption of their equipment to be around 1,300 liters per 100 km or 0.1809 miles per gallon.
Ore movement (haulage) can account for up to 30% of a mining site’s total energy consumption. Diesel fuel alone can account for 3% to 10% of a mine’s total operating expenditures. Some statistics indicate fuel consumption for opencast mining has doubled over the past decade. An article in ‘World Coal’ printed in 2015 identified the top 5 gold producers and calculated the amount of fuel needed to mine an ounce of gold had risen from 12,7 to 21.8 gallons per ounce since 2005. Needless to say, fuel consumption is a main component of mining costs, and increasing fuel efficiency must be a top concern for mining operators.
Fuel Storage Tanks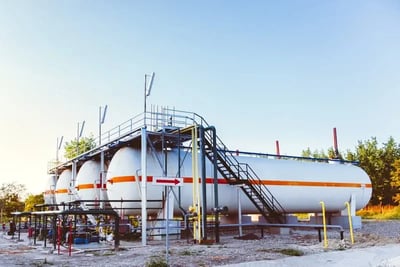
Tight management of fuel storage tanks is mission-critical when considering remote mines. Not only do mining assets consume immense volumes of fuel, the location of some mines also makes the very idea of running out of diesel the stuff of nightmares. Such operations cannot afford to halt all activities while waiting for the next fuel delivery. Fuel storage tanks need to be monitored and managed to within less than 1% accuracy. That may seem like a very small percentage, but taken in the context of millions of dollars of fuel consumption each month, it is 100% appropriate. Therefore, any fuel management system installed at a mine needs to fully integrate electronic tank gauging systems in as automated a way as possible. This will ensure the supply of that vital fuel is not vulnerable to human error and neglect.
Networks and Communication
Closely tied to the remote locations of mines are the challenges fleets may face regarding communication or fleet management and telematics. In the context of fuel management, network availability becomes particularly crucial when managing fuel trucks. In areas where mining vehicles and equipment operate, Wi-Fi and cell coverage are less than guaranteed. This renders any mobile fuel management set-up completely useless if it relies solely on network availability to function. It is, therefore, important to make sure that your tanker truck management system can operate on its own and transfer its data at a later time.
Generators
Another consequence of remote locations is that mines are often off the power grid. This means they are left to generate and manage their own power for… everything! Thus, it is absolutely crucial those generators never run out of fuel. One way to ensure this is to systematically (read “blindly”) include them in periodic fuel runs—an obviously suboptimal strategy. So, on the one hand, deploying fuel trucks to locations where they are not needed wastes time, fuel, and manpower. And on the other hand, not having eyes on each generator’s status and tank level means risking critical issues like fuel leaks and outages.
Clearly, a fuel management system that is well suited to the realities of mining fleets should facilitate just-in-time generator refuelling as well as feature exceptions-based generator status monitoring.
Mining Fleets Need a Robust, Automated, and Intelligent Fuel Management System
Manual logging by operators with subsequent manual transfer of information to spreadsheets for record keeping and analysis leaves much room for human error. These tedious chores are time-consuming and difficult to manage.
And yet, for efficiency improvement initiatives to be successful, it is critical to maintain accurate records to track fuel from initial delivery to the point of consumption. A lack of quality data makes it difficult to correlate fuel consumption with mine ore production adequately. Other important cost analyses, such as fuel consumption by asset, shift, and individual operator personnel, also get hazy. And it becomes difficult to track losses caused by fuel misappropriation.
While fuel management solutions exist for other industries, the mining environment is exceptionally harsh. A solution needs to be not only robust but automatic, intelligent and integrated. It should provide proper real-time data for high-level overviews and the ability to drill down with ease to review fuel consumption at precise mine locations, operation types, time periods, and so on.
Mining: Points to Consider When Shopping for a Fuel Management System
When considering fuel management in the mining sector, there is much more to consider than simply managing pumps in a yard and recording transactions. As in the construction industry, fueling can take place at various locations, from both mobile and fixed storage tanks. But conditions are usually rougher at mines than they are at construction sites. As previously mentioned, the infrastructure in place is often not as accommodating to networks and communication as one would like.
Here are some key points to keep in mind when assessing a fuel management system for a mining operation:
- Automation: there should be as little manual data input as possible. Of particular concern are the inevitable entry errors that come with the human element and shortcuts that decrease data quality—using a single vehicle ID for all fueling transactions, for instance.
- Integration: Fuel management involves several different elements: fuel drops; dispensers, both fixed and mobile; corresponding fixed and mobile tanks; and smaller day tanks. Furthermore, the data captured and generated by the fuel management system must also be used by other applications: ERP, accounting, maintenance, etc. For a system to be suitable for the mining industry, it must not only fully handle all of the fuel management elements listed above but also feature robust integration with other departments’ systems. All of this is necessary to avoid the considerable loss of data integrity that always comes with human recording and manipulation.
- Fuel trucks: in a previous article, we reviewed the importance of tracking fuel end-to-end in the construction industry. The same applies to the mining sector. Many of a mine’s fueling transactions happen in the field and are carried out by mobile storage tanks and dispensers. A worthy mobile fleet fueling software management system must be able to manage and track fuel inventory and distribution in the field. Missing that data would leave a huge gap in your accounting, manual logs come with too many human errors, and relying on disparate systems compromises data integrity, as mentioned above.
- Transfer tanks (aka saddle tanks, aka slip tanks): these tend to be little more than an afterthought and often tracked using manual logs, if at all since the volume of each transfer tank is too small to warrant the same type of fuel management system as the ones found on the bigger fuel trucks. Yet, if a mine utilizes several of these saddle tanks, the fuel distributed really adds up in the aggregate. So the ability to track and manage transfer tanks with a mobile fleet fueling software that automatically and cost-effectively system is a highly desirable feature you should definitely look for in a fuel management system.
- Inventory management and fuel tax recovery: there are staples in fuel inventory management, including recording of deliveries, automated capture of storage tank levels, inventory reconciliation, et al. However, a system must go beyond these basics. This is done to give a complete picture of a mine's fueling activities, of course, but just as importantly, to benefit from fuel tax refunds to the fullest possible extent. The details of fuel tax recovery will vary by jurisdiction, but generally speaking, a system’s fuel inventory management should track and report on the following:
- amount of fuel purchased
- starting and ending balances in the mine’s storage tanks
- amount of fuel used to operate motors for mining operations
- amount of fuel used for heating, electricity, and non-propulsive engines
Also, for period closures to be as accurate as possible, the fuel management system must track fuel transferred for storage (transferred into a truck for delivery from one site to another) and transferred for use (transferred into a truck for distribution but not dispensed yet).
- Redundancy: the system set up at each site and fuel truck must be able to continue operating at all times, even in the event of a network shortage. There should be a copy of the data on a local drive, synched periodically with the central server. This way, fueling operations can continue regardless of network issues without resorting to manual logging and tracking.
Other opportunities for Fuel Savings
There exist many opportunities for reducing a mine’s overall fuel consumption to give profitability a boost.
Much research is being conducted in the areas of better lubricants and additives. For large haul trucks, adjusting key engine control inputs such as shaft positions and boosting pressure and coolant temperatures has greatly improved fuel efficiency. Mining preventative maintenance programs keep equipment running smoothly and production interruptions at a minimum.
As mines dig deeper, haul trucks travel longer distances and at varying increased grades. Improved road surfaces, reduction of road inclines and better haulage routing all contribute to potentially improved fuel efficiency. It is optimum to analyze different mining haulage configurations and document the actual savings in fuel consumption. From that information, a mine can develop routines and methods to reduce fuel consumption. In addition, seasonal weather factors can also be measured to identify and predict periods of higher fuel consumption, and inventory planning can be adapted accordingly.
As there are many opportunities available to reduce fuel consumption, but record-keeping at all usage points must be accurate to assess the effectiveness of any cost improvement project properly. Performance efficiencies and KPIs can be reported in various ways to tell a complete story of a mine's operations.
How Coencorp Can Help
Coencorp has been providing fuel and fleet management solutions for over 30 years. We are no strangers to the mining industry, where our technology is being utilized at opencast mining operations in Northern BC, Ontario, Quebec and in Nunavut. When you need to get precise fuel cost/consumption information to empower you to make better operational decisions, a robust fuel management solution is what you need. The capabilities of Coencorp’s SM2-FUEL include the following:- Accessing critical business planning information and KPIs regarding your fleet and fueling operations through meaningful interactive dashboards in a variety of graphical and tabular user-defined interactive panels.
- Dispensing fuel to all vehicles without compromising accuracy, security or accountability. SM2-FUEL
- Automatically controlling and recording the amount of fuel dispensed from fuel trucks to generators and to other equipment in the field. SM2-FUEL INVENTORY MANAGEMENT
- Always knowing ahead which generators, remote tanks, and equipment need to be fueled, effectively shortening the fuel truck’s fuel runs. SM2-FUEL MOBILE
- Automatically reconciling all the fuel dispensed against all the fuel purchased while getting real-time notification of leak alarms. SM2-FUEL INVENTORY MANAGEMENT
- Controlling all trucks entering and leaving the fuel depot, recording their tanker level and haulage, and authorizing loading arms to dispense fuel to tanker trucks, all automatically with full accountability. SM2-SECURE
- Tracking the fuel being transported from the fuel depot to ensure that it will be delivered to the mine storage tanks. SM2-FUEL MOBILE
- Automatically receiving notifications if a fuel truck or a piece of equipment is entering unauthorized zones or the fuel load is being tampered with during transportation. SM2-LOCATE
- With only a few mouse clicks, access updated views of the total fuel on hand, as well as the current level of each fuel storage tank, fuel tanker, remote day tank and generator operating across the organization. SM2-FUEL
- Running the maintenance operation with maintenance plans that are automatically updated with accurate, critical maintenance planning triggers such as mileage, engine hours and fuel consumption. SM2-MAINTAIN
- Recurring weekly and monthly fleet and fuel reports that are automatically emailed to the recipients of your choice.
- Maintenance work orders are generated automatically; upcoming maintenance notifications are automatically sent; warranties are tracked automatically; and parts inventory is automatically adjusted when a part is consumed, all designed to ensure a longer-lasting, more efficient, and more reliable fleet. SM2-MAINTAIN
Operating an opencast mine consistently and profitably presents many challenges. There are several options available. But when you need to know if your cost-cutting strategies are working, you need a fuel management system that provides automated tracking and accurate data and, thus, the highest confidence in a continually improving bottom line.
Subscribe to The Fleeting thought to be notified of future pieces on fleet management, and leave your comments and questions in the comments section below.